Fabrication
Fabrication Overview
Plastic fabrication makes it possible for a material to be shaped or moulded into different forms and therefore used widely within the industry. There are numerous fabrication methods (depending on the plastic being used), which include compounding or blending, plastic extrusion, plastic welding, and plastic lamination.
Some manufacturers prefer plastic fabrication instead of working with materials such as glass or metal due to the process advantages. A plastic’s cost-effectiveness and malleability can make it a durable and versatile material for a multitude of different products. Its ease of forming, reduced finishing (plastic can be coloured prior to fabrication), faster production and lighter weight are all advantages of plastic versus metal fabrication.
There are considerations when choosing a plastic fabrication process such as the dimensions of the final product, the role of the plastic in the fabrication process, and whether there’s a need for a single versus plastic compounds.
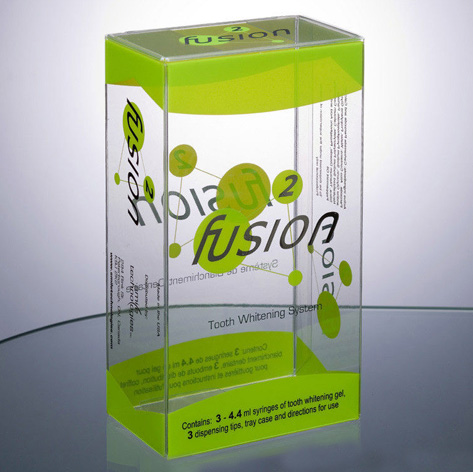
Uses and Limitations
Plastic fabrication (the means by which the material is cut, shaped and formed into an end product), does have distinct advantages and uses. These do depend on the unique characteristics of the plastic being used, so if you are in any doubt, please feel free to ask and we will happily share our knowledge.
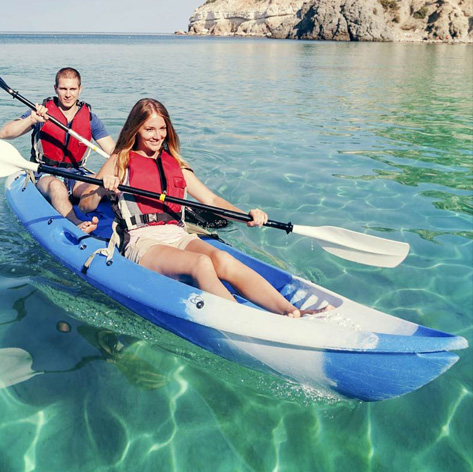
Fabrication Uses
- Ease of forming – due to its high malleability and low melting point, plastic can be fabricated into complex geometries with relative ease.
- Speed – generally plastic fabrication uses quick cycles times and faster turnaround compared to other materials.
- Weight reduction – plastics typically weigh less than other materials, so not only is this a benefit during production but regarding storage and transportation costs too.
- Finishing – unlike metals, thermoplastics can be coloured prior to the fabrication process and can require minimal post-production treatment too.
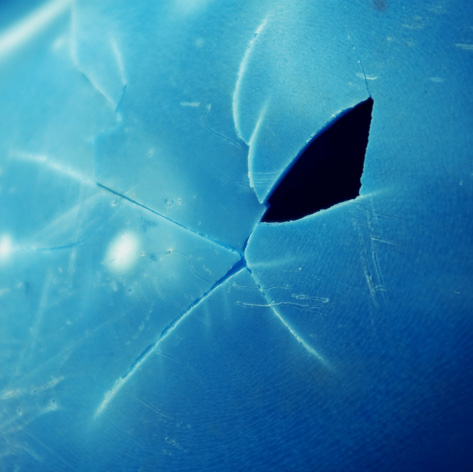
Fabrication Limitations
Plastic fabrication does have its limitations. Structural strength is a consideration as most plastics are unsuitable for heavy use as in equipment components and building materials. The temperature conditions where the product is being used also need to be considered, as does any liquids that may come in to contact as plastic can have a low resistance to acidity or other corrosive substances.